ПОСТРОЙКА "ДЕЛЬФИНА".
Одной из самых больших проблем на катере со стационарным двигателем является проблема герметизации места входа вала в корпус корабля. С этой задачей призван справляться дейдвудный сальник. Сальник можно делать традиционным способом - с сальниковой набивкой, представляющей из себя намотанные на вал кольца специального мягкого пропитанного смазочными веществами жгута, обжимаемые конструкцией сальника на валу до предотвращения течи. Сейчас взамен этой конструкции часто используют обычные резиновые воротничковые манжеты, в просторечии сальники, с которыми знакомо большинство сталкивавшихся с техникой людей. Первый вариант все же предпочтительней в плане надежности - через порванный резиновый сальник вода будет хлестать неостановимо, традиционный сальник в случае течи можно просто зажать сильнее.
Сальник как правило не делается непосредственно на дейдвудной трубе - этот вариант предполагает жесткую фиксацию выходного конца вала в трубе (иначе сальник не выдержит вибраций вала), что приведет к передаче с вала на дейдвудную трубу и всю конструкцию корабля всех вибраций и шума. Поэтому сальник обычно делают в виде независимой конструкции, одетой на вал и соединенной с концом дейдвудной трубы куском дюрита (резино-тканевого шланга). Традиционно (вернее сказать, всегда) основой сальника является выточенная на токарном станке бронзовая разборная конструкция, в случае применения "резиновых изделий" она обеспечивает их плотную установку, наличие контрольного отверстия с пробкой между ними и направляющей бронзовой втулки, которая предохраняет манжеты от смещений вала. Традиционная конструкция представляет из себя точены бронзовый стакан, в который одна за другой входят кольца набивки и сжимающие их распорные и нажимные точеные из бронзы втулки. Сжатие чаще всего осуществляется накручиванием на дальний от винта конец корпуса сальника большой гайки - корпуса нажимной втулки. В прошлом чаще сжатие осуществлялось не гайкой, а винтами, подтягивавшими нажимную втулку с ушами к флянцу сальника.
Токарная работа предполагает наличие токарного станка (у нас его нет), либо использование токаря на стороне, а также наличие большой бронзовой болванки. Под большой болванкой предполагается при нашем валу в 30 мм что-нибудь вроде 10 см диаметра чушки, длиной также сантиметров 10. Это по самым скромным прикидкам. Плюс тот же материал на вытачивание втулок и нажимной гайки. Плюс немалое количество работы токаря. Всё это представлялось как-то не по зубам и карману. Особенно. когда читаешь на форумах, как люди добывают бронзовые болванки по цене в 15 тысяч рублей (500 долларов). Для справки - у нас мотор столько стоит. Короче, решено было делать сальник "на коленке". Сначала я купил пару воротничковых манжет под вал 30 мм и внутренность дейдвудной трубы в 54 мм. Если хотите, можете попробовать повторить мой напрасный подвиг - на белом свете существует только один такой тип сальника - в какой-то конкретной марке стиральных машин. Мы же долго думали, и стали склонятся в сторону традиционной конструкции сальника - с набивкой.
И вот, отец после долгих размышлений, изобрел конструкцию сальника, не отличающуюся от традиционной, но не требующую токарной работы. Ее основа - отрезок трубы, аналогичной дейдвудной (в нашем случае 110 мм диаметр 60 мм внешний, 54мм внутренний, нержавейка). С одного из концов этой трубы мы вварили кольцо из нержавейки. Его задача - удерживать весь пакет сальниковой набивки и втулок при сдавливании. Втулки сделаны из текстолита. Внешний диаметр их - чуть менее 54 мм с тем, чтобы они плотно входили в трубу и центрировались в ней. Внутренний диаметр текстолитовых втулок в районе 30,5-31 мм, отверстия прорезаны фрезером за два прохода двумя фрезами. К сожалению, спиральных фрез для сверления в магазинах города мы не обнаружил, пользовались мало подходящими прямыми фрезами. По внешнему диаметру обрабатывали втулки прямой пазовой фрезой достаточной длины, закрепив фрезер в столешнице.
Заготовку вырезали из пластины с заранее проделанным внутренним отверстием лобзиком с пилкой по металлу. Затем внутрь заготовки шайбы вставляли подшипник с внешним диаметром 30мм (в качестве уплотнения брали бумажную ленточку) и внутренним 10мм - внутрь вставляли винт и крепили подшипник на нем гайкой. Заготовка крепилась на рычаге из полосы толстой фанеры и прижималась к фрезе. Нужно сказать, что при неправильном выборе направления вращения заготовки при обработке, фреза способна временами с силой подхватывать ее и вращать вокруг оси - импровизированное колесо способно поранить руки и остановить его вращение можно только подтормаживая заготовку тем же фанерным рычагом об поверхность стола. Все наши проблемы при обработке тут же исчезли, как только заготовку стали вращать в противоположную сторону. На изготовление четырех шайб - внутренней, 8 мм толщины, лежащей на дне стакана, двух центральных, между которыми будет находится полость для смазки, толщиной по 19 мм каждая и внешней нажимной втулки толщиной 33 мм (для ее обработки понадобилась другая фреза - прежней 20 миллиметровой не хватило, использовали большую 51 мм фрезу под 12 мм цангу) ушло полдня вместе с изобретением метода обработки и конструированием фрезерного стола.
Здесь
И Здесь можно посмотреть видео с выпиливанием втулки из текстолита.
Текстолит в качестве материала был выбран по следующим соображениям - он был в наличии, причем разных толщин - в разной время все куски текстолита были банально найдены на свалке. Текстолит не гниет и не ржавеет, не подвержен старению, как многие пластмассы, не абразивен, как стеклотекстолит (из него наоборот, иногда делают подшипники скольжения), обрабатывается намного лучше металлов, почти на уровне твердых пород дерева, но по прочностным характеристикам ближе к металлам. Внешнее толстое кольцо мы прикрепили латунными винтами М4 к фланцу из нержавеющей стали.
Отверстие во фланце под вал с запасом, чтобы не было касания вала, просверлено коронкой фирмы морзе. Раньше я вообще не пользовался подобным инструментом, а бошевская коронка мне оказалась слишком явно не по карману (при цене около 1200 р за комплект коронка на 30мм - держатель коронок). Морзевская стоила более чем вдвое дешевле, была также изготовлена из кобальтовой стали и справилась с работой на ура. Крутил я ее, естественно, низкооборотной дрелью.
Крепление текстолитовой нажимной втулки к флянцу далось нам с третьего раза - первые две попытки заключались в использовании нержавеющих шурупов и проваливались при скручивании головы очередному шурупу. Приходилось поворачивать втулку на угол и делать новые отверстия. В конце концов это нам надоело и мы просто нарезали в этих отверстиях резьбу и использовали винты.
Заключительным этапом стало приваривание к стакану четырех нержавеющих винтов для скомбинированной из нержавеющего фланца и текстолитовой шайбы нажимной втулки. При сварке резьбу защищали экранчиками из паронита. Предварительно, привернув флянец к доске, сделали через него, как сквозь кондуктор отверстия 5,5 мм толщиной на сверлильной стойке, в них плотно вставили винты с подрезанными на наждаке головками. Это позволило добиться соосности винтов и точности их местоположения при сварке.
Остается нарезать набивку, сжать ее, наметить положение тавотницы, засверлить отверстие под нее и нарезать в нем резьбу, во внутренних текстолитовых шайбах, толщиной по 19 мм проточить надфилем каналы для доступа смазки из пространства между ними к набивке. Между этими втулками будет находится тавотница, а сжаться им не позволит помещенный туда бронзовый сепаратор от подшипника. Его размер позволит ему свободно занять какое-то положение внутри сальника при сдавливании, но не задевать пр этом за вал. Отверстия в нем позволят смазке свободно заполнить всю полость.
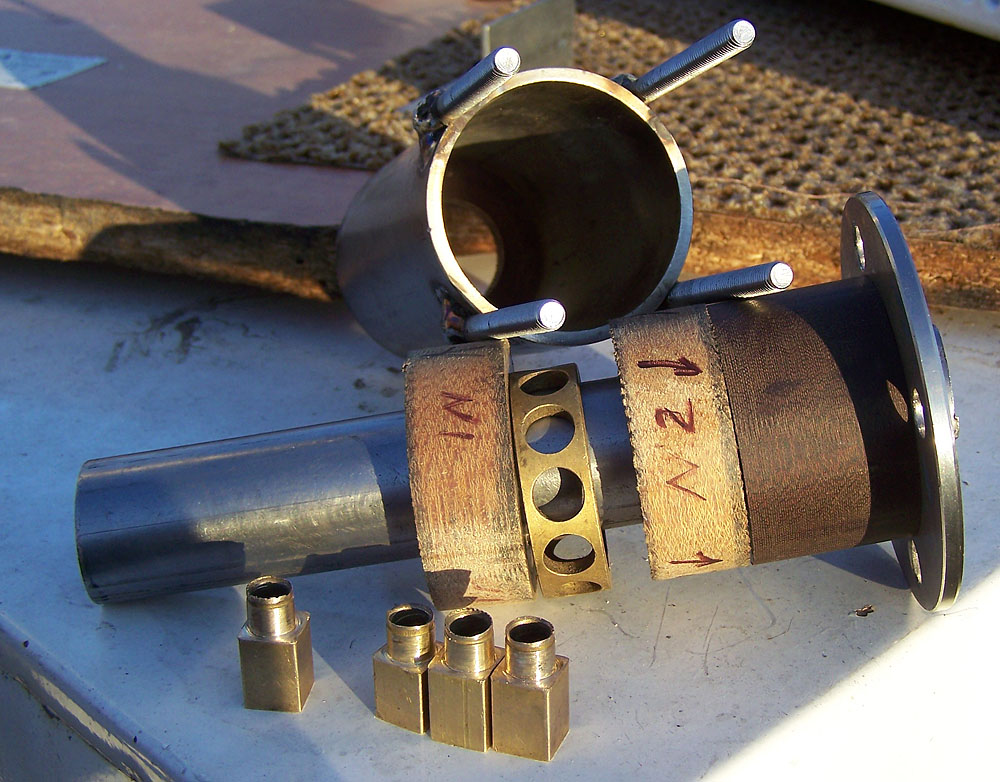
В НАЧАЛО
На следующую
Эпилог